Understanding Injection Molding Tools: A Comprehensive Overview
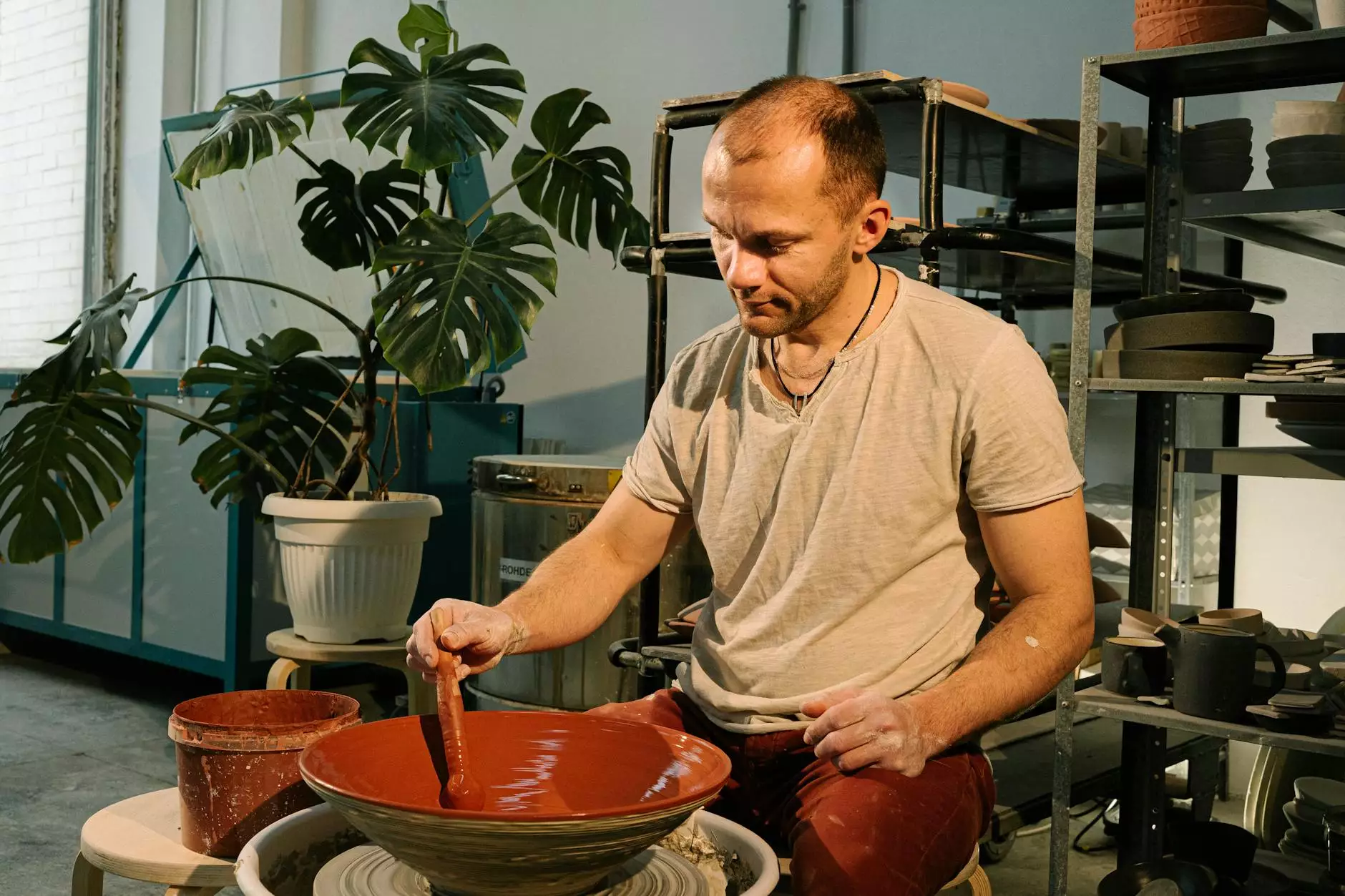
Injection molding tools represent a cornerstone in the world of manufacturing, particularly within the realm of metal fabrication. The precision and efficiency that these tools offer can dramatically enhance productivity and quality in production processes. In this article, we will delve into the complexities and advantages of injection molding tools, and how they are integral to manufacturers seeking high-quality results.
The Basics of Injection Molding
At its core, injection molding is a process used to produce parts by injecting molten material into a mold. This method is especially popular in producing complex shapes with high precision. The injection molding process involves several stages:
- Material Selection: The choice of material, typically thermoplastics or thermosetting polymers, is crucial as it affects the final product's properties.
- Melt Phase: The raw material is heated until it becomes a molten state suitable for injection.
- Injection Phase: The molten material is injected into the prepared mold under high pressure.
- Cooling Phase: The injected material is allowed to cool and harden within the mold.
- Demolding Phase: Once cooled, the mold is opened, and the part is ejected.
Importance of Injection Molding Tools
Injection molding tools are critical components of the manufacturing process. These tools not only shape the completed products but also play a vital role in ensuring that each item meets the required specifications. Let’s explore some reasons why these tools are indispensable:
1. Precision and Reproducibility
One of the standout features of injection molding tools is their ability to produce parts with extraordinary precision. This is particularly important in industries where dimensions and tolerances are critical, such as in the automotive or aerospace sectors. The injection molding process ensures that each piece produced is identical, reducing waste and the need for extensive quality control checks.
2. Efficiency in Production
The speed at which injection molding tools can operate is a major asset for manufacturers. With the ability to produce thousands of identical units within a short timeframe, businesses can scale their production without compromising quality. This efficiency not only reduces costs but also shortens lead times, allowing companies to respond quickly to market demands.
3. Versatility in Manufacturing
Injection molding tools can be used with a wide variety of materials beyond plastics, including metals and composites. This versatility allows manufacturers to tailor their production processes to specific requirements, making injection molding tools suitable for a diverse range of applications—from consumer goods to complex machinery components.
Types of Injection Molding Tools
Understanding the different types of injection molding tools can help manufacturers select the right equipment for their specific needs. Here’s a look at some common types:
1. Single Cavity Molds
Single cavity molds are designed to produce one part per cycle. They are ideal for small production runs or prototypes, where cost pressure is lower and flexibility is necessary.
2. Multi-Cavity Molds
Multi-cavity molds allow for the simultaneous production of multiple parts. This type of tool increases production speed and efficiency, making it a popular choice for high-volume manufacturing.
3. Family Molds
Family molds are designed to produce several different parts in one cycle. Each cavity produces a different piece, allowing for greater variation in products and reducing the amount of tooling needed.
4. Hot Runner Molds
Hot runner molds keep the plastic material in a molten state within the mold, reducing waste and improving cycle times. These molds are particularly efficient for large-scale production.
5. Cold Runner Molds
Cold runner molds use a different approach where the plastic cools in a channel before injection. While they are less efficient than hot runner molds, they can be more economical for certain applications.
Factors to Consider When Selecting Injection Molding Tools
Choosing the right injection molding tools involves several considerations to ensure optimal production efficiency:
- Material Compatibility: Ensure that the tool can accommodate the specific materials being used.
- Mold Design: Consider the complexity of the part design and choose a mold that can replicate intricate features.
- Cycle Time: Analyze production speeds to ensure that the tools can meet output demands.
- Budget Constraints: Evaluate the costs associated with both the initial investment in tooling and the ongoing operational expenses.
Maintenance of Injection Molding Tools
Regular maintenance of injection molding tools is essential for long-term productivity and efficiency. Neglecting this aspect could lead to increased wear and potential faults in the production process. Here are some key maintenance practices:
1. Routine Inspections
Regularly inspect molds for signs of wear, damage, or contamination. Addressing minor issues before they escalate can save considerable costs and downtime.
2. Cleaning Protocols
Implement stringent cleaning protocols to ensure that molds are free from residue and buildup. Utilizing appropriate cleaning solutions and methods can extend the tool's lifespan.
3. Lubrication
Proper lubrication of moving parts is crucial to reduce friction and wear. Utilize manufacturers’ recommendations for lubrication intervals and types.
The Future of Injection Molding Tools
The landscape of injection molding tools is continuously evolving with advancements in technology. Innovations such as:
- 3D Printing: Integration of 3D printing technologies to create mold prototypes quickly.
- Smart Molding: Incorporating IoT capabilities for real-time monitoring of the injection molding process.
- Sustainable Practices: Adopting eco-friendly materials and processes tailored to reduce waste and environmental impact.
Conclusion
Injection molding tools are undoubtedly a vital component in the world of manufacturing and metal fabrication. Their precision, efficiency, and versatility make them an essential part of countless production processes. As manufacturers at DeepMould.net continue to seek methods to enhance the efficiency and quality of their operations, understanding and leveraging the advantages of these tools will be crucial for maintaining a competitive edge. By investing in the right technology and practices, businesses can ensure sustainable growth and success in the increasingly demanding manufacturing landscape.