The Comprehensive Guide to Plastic Injection Molds
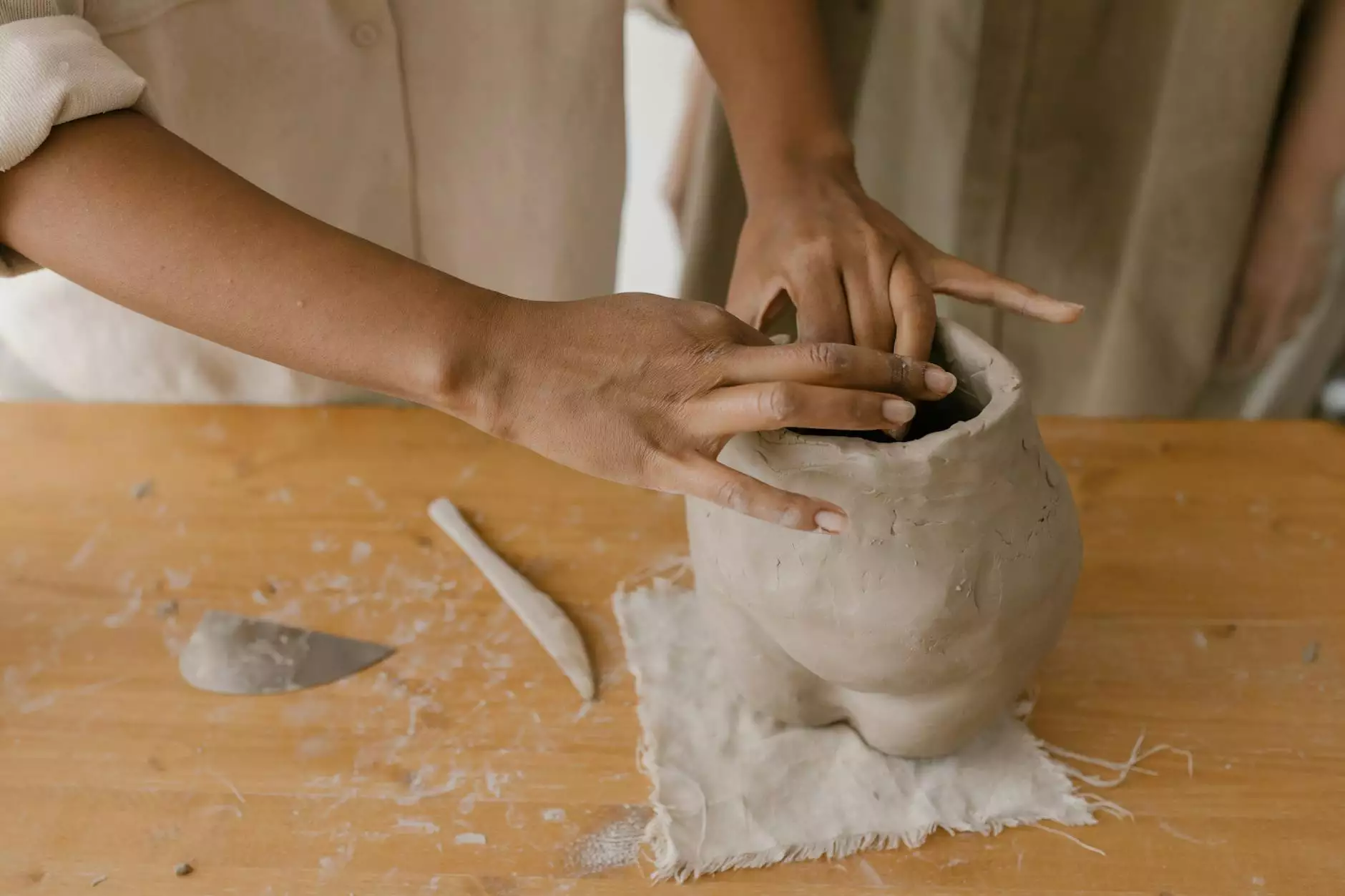
In today’s fast-paced manufacturing landscape, plastic injection molds have emerged as a pivotal technology for creating intricate plastic parts with precision and efficiency. This article explores the importance, applications, and advantages of plastic injection molds, particularly in the domain of metal fabricators.
Understanding Plastic Injection Molding
Plastic injection molding is a manufacturing process that involves injecting molten plastic into a mold cavity. The solidified plastic then takes the shape of the mold, enabling the production of a vast array of products. This method is favored for its speed, repeatability, and the ability to create complex geometries.
The Anatomy of a Plastic Injection Mold
A plastic injection mold consists of several key components that work harmoniously to produce high-quality parts. These components include:
- mold base: The foundation that holds the entire mold assembly.
- Cavity: The hollow space that defines the part's shape.
- Core: The component that forms the inner features of the part.
- Cooling system: Channels that allow for temperature regulation to optimize production cycles.
- Ejection system: Mechanisms that facilitate the removal of the part from the mold after cooling.
Benefits of Using Plastic Injection Molds
The use of plastic injection molds offers numerous benefits for manufacturers, including:
- High Efficiency: Once a mold is created, the speed of production is significantly increased, allowing for large quantities to be produced quickly.
- Cost-Effectiveness: The ability to produce parts in bulk reduces the overall cost per unit.
- Precision and Accuracy: The process allows for tight tolerances and complex designs, ensuring consistent quality.
- Material Variety: A wide range of thermoplastics and thermosetting plastics can be used, allowing for specialized applications.
- Minimal Waste: The process is designed to use plastic efficiently, generating little to no waste material.
Applications of Plastic Injection Molding
Plastic injection molding is utilized in various industries, showcasing its versatility and effectiveness. Some common applications include:
- Automotive Parts: Dashboard components, interior trim, and even engine components.
- Consumer Electronics: Covers, casings, and intricate internal components.
- Medical Devices: Precision parts such as syringes, housings, and various disposable items.
- Household Goods: Kitchenware, toys, and home improvement products.
- Industrial Equipment: Parts for machinery, safety equipment, and hardware.
Key Considerations for Designing Plastic Injection Molds
Creating an efficient plastic injection mold requires careful design and consideration. Here are some crucial factors to keep in mind:
1. Material Selection
Selecting the appropriate plastic material is critical. Factors including strength, flexibility, and heat resistance will dictate the choice of resin.
2. Mold Design
The mold must be designed with the manufacturing process in mind, ensuring easy ejection and uniform cooling.
3. Tolerances
Understanding the required tolerances for the final product will guide many design decisions and ensure quality.
4. Injection Speed and Pressure
Controlling these variables is essential to prevent defects such as warping or incomplete filling.
Maintenance of Plastic Injection Molds
Like all machinery, plastic injection molds require regular maintenance to extend their lifecycle and maintain performance. Key maintenance practices include:
- Regular Cleaning: Keeping molds free from contaminants that can affect part quality.
- Inspection for Wear: Periodically checking for damage or wear and addressing issues promptly.
- Lubrication: Ensuring all moving parts operate smoothly to prevent breakdowns.
The Future of Plastic Injection Molding
As technology advances, the future of plastic injection molds looks promising. Innovations such as:
- 3D Printing: Used for rapid prototyping of molds.
- Smart Molding Technologies: Integration of IoT for real-time monitoring and adjustments.
- Eco-Friendly Materials: Development of biodegradable and recycled plastics for sustainable practices.
Conclusion
In conclusion, plastic injection molds play an indispensable role in modern manufacturing, particularly within the metal fabricators industry. With their numerous benefits, diverse applications, and advances in technology, businesses like deepmould.net are uniquely positioned to leverage these tools for efficient production processes. By understanding the intricacies of plastic injection molding, manufacturers can ensure high-quality products while meeting market demands effectively.